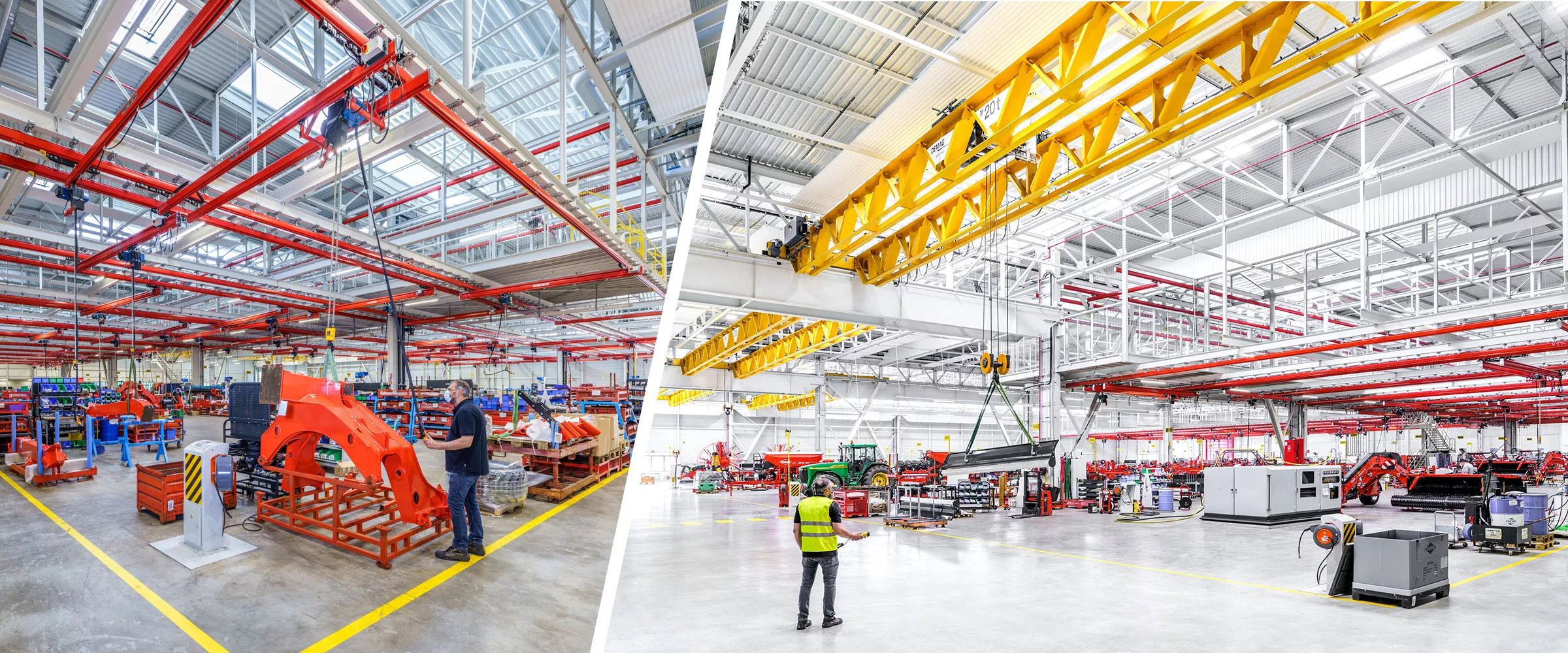
Landmaschinen aus dem Norden Frankreichs
Flexibler und modularer Materialfluss
V-Profilkrane und 3,2 km KBK-Profile mit 120 Kettenzügen DC für KUHN MGM SAS
Die Unternehmensgruppe KUHN
Im Nord-Osten Frankreichs, in der Nähe von Straßburg, ist einer der weltweit führenden Hersteller von Landmaschinen beheimatet. Die KUHN Unternehmensgruppe verspricht den Landwirten Innovationsstärke und Qualität zu marktgerechten Preisen. An diesem Versprechen arbeiten mittlerweile über 5000 Mitarbeiter weltweit an zahlreichen Produktions- und Vertriebsstandorten.
Aus dem Elsass in die Welt
Begonnen hat das Unternehmen mit seinem Gründer und Namensgeber Joseph Kuhn im Jahr 1828 als Dorfschmiede. Die Schmiede spezialisierte sich bald darauf Waagen und Messinstrumente zu fertigen. Ein Umzug des Firmensitzes nach Saverne erfolgte im Jahr 1864 und damit die Spezialisierung auf den Bau landwirtschaftliche Geräte. Seither wird in der Region Saverne, und der dazugehörigen Gemeinde Monswiller, an der Weiterentwicklung von Mähwerken, Heuwendern, Schwadern, Häckslern sowie an Geräten zur Bodenbearbeitung und Sämaschinen gearbeitet.
Die Aufgabe
Die Produktion im Hauptwerk in Saverne wurde in den vergangenen Jahrzehnten mehrfach erweitert und an die stetig steigende Nachfrage nach immer größer werdenden Landmaschinen angepasst. Die Flurbreiten von maximal 15 Metern limitierten jedoch die Produktion, so dass vor einigen Jahren ein neues Montagewerk in der angrenzenden Gemeinde Monswiller errichtet wurde. Das Kürzel „MGM“ steht für „Montage Grande Machine“ und erklärt, dass Flurbreiten von bis zu 20 Metern notwendig sind, um die Landmaschinen der neueren Generation zu montieren. KUHN errichtete eine moderne Produktionshalle für die Fließfertigung von großen Landmaschinen.
Insgesamt wurde das Montagewerk um 20.461 m² erweitert. Im Detail gliedert sich die Erweiterung auf in 11.065 m² für eine neue Montagehalle, 5.437 m² für eine Erweiterung der Logistikhalle sowie 3.017 m² für eine Versandhalle. Zusätzliche Außenflächen und der Neubau einer Kantine komplettieren das Werksgelände.
Effizientes Fertigungslayout
Das Hauptwerk in Saverne produziert kleinere Landmaschinen und Komponenten für den MGM in Monswiller. Hier werden die größeren Maschinen montiert, die für die Heuernte, Bodenbearbeitung und zum Säen eingesetzt werden.
Diese Komponenten werden ebenso wie die Zukaufteile im Wareneingang, dem „Magasin“, kommissioniert und den Montagelinien zugeführt. Jeden Monat kommissioniert der Bereich circa 100 Tonnen Material.
Zukaufteile und andere Komponenten werden in der hauseigenen KTL-Lackiererei pulver- und lackbeschichtet. Innerhalb der Linien erfolgt die Montage: An den einzelnen Montageplätzen werden die Landmaschinen Schritt für Schritt aufgebaut und nach der Endmontage sowie einem Funktionstest für den Versand vorbereitet.
Seitlich der Montagelinie sind Anlieferbereiche für die Intralogistik. Die Mitarbeitenden benötigen eine flurfreie Lösung zum Transport der angelieferten Ware aus dem Magasin und der Lackiererei hin zur Montagestätte. Darüber hinaus ist das Materialhandling an den einzelnen Arbeitsplätzen von entscheidender Bedeutung, um die Bauteile präzise miteinander zu verknüpfen und den Mitarbeitern das Handling so leichtgängig wie möglich zu gestalten. Bei der Montage der Baugruppen an das Hauptgestell der Landmaschine sind Präzision des Hebezeugs bei der Positionierung und der Steuerung von immenser Bedeutung für das effiziente Arbeiten. Leichtkrane sind daher für jeden Arbeitsschritt essenziell.
Am Ende der Fertigungslinie unterstützen Universalkrane bei der Endmontage. Je nach Art und Größe der Landmaschinen werden sperrige und schwere Komponenten am Hauptgestell montiert und müssen daher ebenfalls aufgenommen und positioniert werden. Zuletzt erfolgt ein Funktionstest und die fertigen Landmaschinen werden in die neu errichtete Versandhalle transportiert. Dort angekommen übernehmen Krane die Beladung der Lkw.
Die Lösung
Die Erweiterung der Fertigung geht einher mit der Ausweitung des Materialflusskonzepts bei KUHN MGM: 9 Laufkrane vom Typ ZVKE mit V-Profil und einer jeweiligen Tragfähigkeit von 20 Tonnen sowie 120 Kettenzüge vom Typ DC-Pro unterstützen entlang der neuen Montagelinien und im Versand. Mit einer Erweiterung um 3,2 Kilometer KBK Profilen, werden auch die neuen Montagelinie vollends mit dem Leichtkransystem überspannt.
KUHN MGM und Demag in Frankreich haben die Anlieferungen terminiert, so dass die neuen Krane abschnittsweise und termingenau montiert werden konnten. Die Montage der Leichtkransysteme erfolgte, nach eingehender Schulung, durch die Mitarbeiter der eigenen Instandhaltung.
Modular, sicher und effizient: Das Leichtkransystem KBK
Entlang der Montagelinien in Monswiller erstreckt sich ein dichtes Netz des Leichtkransystems KBK am Himmel der Produktionshalle. Die Mitarbeiter verfahren die einzelnen Komponenten der Landmaschinen mit KBK Ein- und Zweiträgerkrane flurfrei von der Logistiklinie zu den Montageplätzen der ca. 100 Meter langen und 25 Meter breiten Fertigungslinien. Bei der Werksplanung wurde darauf geachtet, dass KBK absolut flächendeckend verbaut und damit bei jedem Arbeitsschritt zur Unterstützung verfügbar ist.
Als Hebezeuge werden DC-Pro Kettenzüge eingesetzt, die bei Tragfähigkeiten von bis zu 1000 kg per Hand und darüber hinaus, bei bis zu 2000 kg Tragfähigkeit, elektrisch verfahren werden. Der Transport der Komponenten erfolgt mit beiden Antriebsarten absolut leichtgängig am Montageplatz, so dass die Landmaschinen effizient und ergonomisch montiert werden können. Gelenkverbindungen zwischen Kranträger und Fahrwerk ermöglichen ein leichtgängiges Materialhandling der vormontierten Baugruppen vom Montageplatz zum Maschinengestell. Die teils stufenlosen und niedrigen Geschwindigkeiten der DC-Pro Kettenzüge helfen den Kranbedienern dabei die Baugruppen bei der Montage einfach und präzise auszurichten. Die Einpassung einer sperrigen Walze für die Bodenbearbeitung kann somit gleichermaßen ausgeführt werden wie das Einpassen einer Elektronik- oder Hydraulikeinheit.
Komfort und Sicherheit beim Lasthandling mit dem Kettenzug DC-Pro
Die Kompatibilität der Demag Komponenten untereinander bietet KUHN MGM sogar die Möglichkeit Kettenzüge älterer Generation aus dem Bestand, zum Beispiel des Typs DK oder gar PK, einzusetzen. Die Mitarbeiter haben sich jedoch an die Vorzüge der neuesten Generation des Typs DC-Pro gewöhnt: Die Positionierung der Komponenten erfolgt mit zwei Geschwindigkeiten auch bei niedrigen Geschwindigkeiten absolut präzise. Mit Tragfähigkeiten von 500 bis 2000 kg und einem einheitlichen Hakenweg von 5 Metern können die Kettenzüge an allen Arbeitsplätzen flexibel eingesetzt werden. Die höhenverstellbare Steuerleitung des einheitlich gewählte Steuerschalter DSC bietet größte Ergonomie. Die ergonomische Griffform sowie die mangelnde Umgewöhnung bei einem Wechsel des Arbeitsplatzes, steigern die Effizienz bei der Montage.
Der Kettenzug DC-Pro verfügt mit Getriebe, Rutschkupplung und Bremse über hochwertige Komponenten, die bis zu 10 Jahre wartungsfrei sind. In Kombination mit der automatischen Abschaltung der Rutschkupplung und der automatischen Bremsung bei einem Steuerungsausfall, können sich die Mitarbeiter von KUHN auf den zuverlässigen DC-Pro an ihrem Arbeitsplatz verlassen. Die Sicherheitsbezogenen Funktionen des Kettenzugtyps erfüllen mindestens Performance Level c und Kategorie 2 nach EN ISO 13849-1.
Absolute Betriebssicherheit bei hoher Effizienz
Die neun gelieferten Zweiträger-Laufkrane ZVKE mit V-Profil bieten ebenso höchste Betriebssicherheit und Effizienz. Die Membrangelenke des Kranträgers ermöglichen das lichtdurchlässige V-Profil-Design. Durch den verringerten Materialbedarf hat der innovative Kranträger ein geringeres Eigengewicht, welches sich positiv auf die Statik der Halle auswirkt. Die Spannweiten der Laufkrane erstrecken sich 10,4 Metern bis 28,3 Metern.
„Ich habe den Kran zum ersten Mal bei einem anderen Kunden von Ihnen gesehen und war gleich beeindruckt. Den Kranträger sieht man fast gar nicht, er lässt so viel Licht in die Halle. Auch dadurch hat man den Eindruck, dass der Kran sehr leicht ist.“ - Stéphane Schissele, KUHN SAS
Mit einer Tragfähigkeit aller Krane von jeweils 20 Tonnen kann KUHN MGM mit Sicht auch in Zukunft größere und schwerere Landmaschinen für die Endmontage anheben und zum Versand transportieren. Fünf Krane unterstützen am Ende der Produktionslinie die letzten Montageschritte, um die vormontierten und nun erheblich schwereren Komponenten miteinander zu verheiraten. Nicht nur Hubkraft, sondern vor allem die präzise Positionierung der Komponenten dank der stufenlosen Steuerung stellen eine enorme Arbeitserleichterung dar.
Weitere vier ZVKE sind im neu errichteten Versandbereich eingesetzt und verladen die fertig gepackten Komponentenpakete und Landmaschinen auf Lkw. Der Versand aus Monswiller erfolgt an Kunden in der ganzen Welt.
Der modulare Demag Seilzug DMR ermöglicht die Einbindung von mechanischen und elektrischen Hilfestellungen. Die frequenzgeregelte Steuerung der Krane spielt beim Komfort eine wichtige Rolle und lässt die Bediener im Versandbereich die Paletten mit Landmaschinenkomponenten oder ganze Landmaschinen präzise aufnehmen und verfahren. Anfahrt und Beschleunigung erfolgen stufenlos, so dass der Bediener Kran-, Katz- oder Hubbewegung präzise steuern und sich beim Verladen auf das Ausnutzen des Laderaums im Lkw konzentrieren kann.
Gesicherter Kranbetrieb
Bei allen neun Kranen überwacht und sichert die intelligente Sicherheitssteuerung SafeControl den Betrieb jederzeit ab. Eine zweistufige Abschaltung verhindert das Auffahren des Krans sowie der Katze auf die Endanschläge. Mit Erreichen des ersten Endschalters, schaltet die Kran- oder Katzfahrt in die Feinfahrt-Geschwindigkeit. Sobald der zweite Endschalter erreicht wird, werden die Kran- oder Katzfahrtantriebe abgeschaltet und die Fahrt wird sanft abgebremst. Ein Lastpendeln wird durch die Kombination aus stufenloser Steuerung und Endschaltern vermieden, so dass die Ladung keinen Schaden erleidet und auch keinen Schaden am Lkw oder in der Umgebung anrichtet. Der Kranbediener profitiert von der elektronischen Hilfestellung und wird bei unvorhersehbaren Situationen vom Kran unterstützt und abgesichert.
Zwei der ZVKE verfahren im neuen Fertigungsabschnitt auf einer Kranbahn. Zur Vermeidung von Kollisionen wird eine optischen Krandistanzierung eingesetzt: Doppel-Lasersensoren messen redundant die Distanz zwischen den jeweiligen Kranen auf der Kranbahn und beim Überschreiten vorab definierter Abstände wird der jeweilige Kran zweistufig und gesichert abgeschaltet. In der ersten Stufe ist der Kran nur noch in langsamer Geschwindigkeit zu verfahren, im zweiten Schritt schaltet der Kran gesichert ab. Dieses Konzept der eigenständigen Sicherheitsabschaltung mit zweikanaliger Hardware entspricht der Sicherheitskategorie 3 nach EN 13849-1.
Betriebszustände stets im Blick
Das Gewicht der Last im Haken hat der Bediener auf dem Demag StatusBoard am Kranträger stets im Blick. Darüber hinaus visualisiert das StatusBoard in Echtzeit die aktuellen Betriebszustände des Krans. Dies sind beispielsweise Traglast, Summenlast, Überlast, Service-Informationen oder die aktivierten Assistenz- und Komfortfunktionen der Sicherheitssteuerung SafeControl - transparenter und vor allem sicherer Kranbetrieb.
Die Besonderheiten
Der modulare Kranbaukasten KBK ermöglicht KUHN MGM die Realisierung der gewünschten Arbeitsplatzbekranung und kann bei Bedarf jederzeit erweitert werden. Kranbahnen sowie Säulen- und Wandschwenkkranen transportieren die Komponenten flächendeckend. Die KBK Ausführungen aus Stahl und Aluminium sind gleichermaßen für diverse Anforderungen geeignet und können auch nachträglich noch kombiniert werden.
Die Leichtgängigkeit der Demag Komponenten ermöglicht zügiges und sicheres Handling und gleichzeitig exaktes, müheloses Positionieren der Einzelteile zur Montage. Damit sorgt das Leichtkransystem für effektive Arbeitsabläufe und erhöht die Produktivität und Effizienz.
Die V-Profil Konstruktion mit Membrangelenken ermöglicht die Einsparung von Eigengewicht und wirkt sich somit positiv auf die Hallenstatik aus. Die intelligente Sicherheitssteuerung SafeControl bietet größtmögliche Sicherheit beim Kranbetrieb. Kranfahrendschalter und die optische Distanzierung der Krane unterstützen den Bediener elektronisch und helfen bei der Vermeidung von ungewollten Schäden im Arbeitsumfeld des Krans. In Kombination mit der stufenlosen Steuerung der Kran- und Katzfahrt sowie der Hubbewegungen, wird die Kranbedienung komfortabler.
Interview
Wir führten ein Interview mit Stéphane Schissele, Gebäude und Wartungsmanager, bei KUHN MGM SAS in Monswiller, Frankreich.
Demag: Herr Schissele, könnten Sie bitte das Unternehmen KUHN MGM SAS und den Standort ins Monswiller kurz vorstellen?
Stéphane Schissele (KUHN MGM SAS): Monswiller befindet sich im Département Bas-Rhin und damit im Elsass. Unser Unternehmen ist in dieser Region fest verwurzelt und mittlerweile mit zwei Standorten in Saverne und Monswiller vertreten. Das Produktions- und Montagewerk in Saverne ist der Hauptsitz der KUHN-Gruppe. In Monswiller beheimatet sind das Montagewerk MGM sowie die Fertigung der Ersatzteile. Die Erweiterung „MGM“ setzt sich aus „Montage Grande Machine“ zusammen. Hier werden die größeren Landmaschinen montiert.
Das Montagewerk wurde 2008 mit vier Montagelinien eröffnet und hatte bisher einen jährlichen Output von 9.000 Maschinen. Mit der Erweiterung wurde die Kapazität am Standort verdoppelt. Mittlerweile fertigen 350 Beschäftigte Landmaschinen für die Heuernte, Bodenbearbeitung und Saatmaschinen. Darüber hinaus ist MGM spezialisiert auf die Produktion saisonaler Maschinen.Demag: Aus welchen Gründen wurde die Investition am Standort notwendig?
M. Schissele: Zuerst war es uns wichtig, dass wir die Fertigungskapazitäten von vormals vier auf acht Montagelinien erhöhen konnten. Dazu passend konnten wir eine eigene Fläche für die Logistik ergänzen und den Fertigungsprozess mit einer neuen Versandhalle in Monswiller abrunden.
Darüber hinaus ist es unser Anspruch, uns dynamisch an die wechselnden Anforderungen unserer Kunden anpassen zu können. Vor einigen Jahren kamen wir in Saverne mit Flurbreiten von 14 oder 15 Metern Arbeitsbreite aus. Diese wurden über die Jahre jedoch zu knapp, so dass wir an diesem Standort mittlerweile 20 Meter Arbeitsbreite an den Montagelinien haben. Das ist für uns immens wichtig, da die Maschinen immer größer und breiter werden. Die Produktion benötigte daher mehr Platz.
Aus diesen Gründen war der Neubau des Werks sowie die jüngste Erweiterung für uns essenziell und bietet die passende Produktionsumgebung für die kommenden Jahre.Demag: Können Sie uns ein Gefühl für die Größenordnung der Erweiterung geben?
M. Schissele: Wir haben eine Erweiterung von knapp 20.000 m² für produktive Bereiche wie Montage, Logistik und Versand durchgeführt.
Demag: Welche Aufgaben erfüllen die Demag Produkte?
M. Schissele: Demag Produkte übernehmen das Materialhandling an den verschiedenen Arbeitsplätzen im gesamten Werk. Das Leichtkransystem KBK erfordert wenig Kraftaufwand unserer Mitarbeiter beim Transport der Bauteile in unserer KTL-Lackiererei und bei der Vormontage. Die in den KBK-Anlagen verbauten Kettenzüge haben zumeist eine Tragfähigkeit von 500 kg bis 1000 kg und werden für das Handling und die Positionierung der Komponenten im Rahmen der Montage eingesetzt. Sind die Baugruppen vormontiert, benötigen wir die Hebezeuge, um die Baugruppen zum Hauptgestell der Maschine zu transportieren. Die teils stufenlosen und niedrigen Geschwindigkeiten der Demag DC-Pro Kettenzüge helfen unseren Mitarbeitern, die Baugruppen der Montage einfach und präzise auszurichten.
„Präzise Montage der Baugruppe dank der stufenlosen und niedrigen Geschwindigkeiten der Demag DC-Pro Kettenzüge“
Am Ende der Montagestraßen erfolgt die Endmontage der Maschinen mithilfe von V-Profilkrane mit 20 Tonnen Tragfähigkeit.
Demag: Welche konkreten Anforderungen hat KUHN an die Produkte von Demag gestellt?
M. Schissele: Für uns ist die hohe Betriebssicherheit der Komponenten enorm wichtig, damit eine optimale Sicherheit für das Bedienpersonal gewährleistet wird. Dadurch dass wir bereits seit mehrere Jahrzehnten Partner von Demag sind, ist uns die Langlebigkeit der Produkte bekannt und diese fordern wir auch ein.
Demag: Weshalb hat KUHN die Arbeitsplatzlösungen von Demag präferiert?
M. Schissele: In Saverne betreiben wir noch eine sehr große Flotte von Hebezeugen der Generation PK (a.d.Red.: Kettenzüge der Baureihe PK wurde von 1961 bis 1995 gefertigt). Die Langlebigkeit der Produkte ist daher bei uns bestens bekannt. In den vergangenen Jahrzehnten sind Kettenzüge der verschiedensten Generationen täglich im Gebrauch und weiterhin voll funktionstüchtig. Wenn sich die Mitarbeiter für stufenlose Hubgeschwindigkeiten am Arbeitsplatz aussprechen, modernisieren wir die Hebezeuge mit Geräten der neuen Generation DC. Wir haben andere Produkte getestet, aber die Geschwindigkeit bei Demag Produkten ist perfekt einstellbar, so dass das Einpassen der Komponenten hundertprozentig stimmt. Der Zugewinn an Präzision ist bei Demag Hebezeugen absolut gegeben.
„Der Zugewinn an Präzision ist bei Demag Hebezeugen absolut gegeben.“
Ein weiterer Grund ist, dass man die Produkte gut per Hand bewegen kann. Die Hebezeuge verfahren bei uns fast ausschließlich an mehreren Kilometern KBK-Schienen. Wie bereits erwähnt, haben die Kettenzüge bis zu 1000 kg Tragfähigkeit, so dass man meinen könnte der Transport per Hand könnte schwierig werden: die Leichtgängigkeit von KBK ist aber tatsächlich enorm! In Saverne und Monswiller können jedoch Lasten bis zu 1000 kg und Spannweiten bis zu 7 Metern problemlos manuell verfahren werden. Wenn wir von Lasten über 2000 kg oder mehr sprechen, ist natürlich ein elektrischer Antrieb notwendig.
„(…) die Leichtgängigkeit von KBK ist aber tatsächlich enorm!“
Für die Planung und Flexibilität der Produktion ist es ebenso unabdingbar, dass wir die Anordnung der Arbeitsplätze anpassen können. Die Änderung oder Erweiterung der KBK-Anlagen ist jederzeit möglich und teilweise werden 30 oder 40 Mal pro Jahr die Krane auf einzelnen Produktionslinien demontiert und neu montiert, um beispielsweise in eine andere Richtung zu fahren. Das KBK-System ist hier in Monswiller so verbaut, dass möglichst viel Fläche abgedeckt werden kann. Wir können nie vorab sagen, ob die Montagelinie acht oder zehn Tage dieselbe bleibt. Die Anforderungen können sich sogar täglich ändern. Vor 20 Jahren wurden 1000 Maschinen auf einer Linie montiert, mittlerweile sind es vielleicht 80, 60, 50, manchmal nur 40 Maschinen. Die Serien werden kleiner und kleiner, das heißt die Linien müssen flexibel bleiben. Und natürlich genauso die Kranbahnen.
Die Lösung, die wir seit über zwei Jahrzehnten mit KBK einsetzen, ist die beste Lösung für uns. Wir kommen mit den Teilen nah an die Linie und die Mitarbeiter können sich die Komponenten zur Montage leichtgängig an den Arbeitsplatz transportieren. Dies geht von Arbeitsplatz zu Arbeitsplatz und entlang der 100 Meter langen Fertigungslinien, bis wir am Ende der jeweiligen Linie die fertige Landmaschine testen und für den Versand vorbereiten können. Zur Endmontage und für das Handling der fertigen Produkte unterstützen Demag V-Profilkrane.
Demag: Wie gefällt Ihnen das V-Profildesign der Kranträger?
M. Schissele: Das ist wahrlich eine Neuheit. KBK kennen wir bereits seit Jahren, aber das V-Profil bei den Kranen ist wirklich eine Innovation. Ich habe den Kran zum ersten Mal bei einem anderen Kunden von Ihnen gesehen und war gleich beeindruckt. Den Kranträger sieht man fast gar nicht, er lässt so viel Licht in die Halle. Auch dadurch hat man den Eindruck, dass der Kran sehr leicht ist.
Auf den Stahlbau der Halle hat das geringe Eigengewicht natürlich einen positiven Effekt. Dazu ist das Design absolut ästhetisch. Wenn man sich dazu noch die technischen Angaben ansieht und die mögliche Tragfähigkeit und Geschwindigkeit, trotz des geringen Eigengewichts, erkennt, dann muss ich sagen, dass das ganz schön beeindruckend ist. Das spiegelt sich natürlich im geringeren Verschleiß der Laufräder und der Fahrbahnen wider und ist für uns dann ein positiver Kosteneffekt. Wir hatten uns auch Anlagen von Konkurrenten durchrechnen lassen, diese sind durch die herkömmlichen Kranprofile jedoch schwerer und höher, wodurch die Kranbahn viel höher gewesen wäre. Der Unterschied betrug zum Teil bis zu einem Meter. Das hat bei uns einfach nicht gepasst und wir haben uns daher für das innovative Design entschieden.
„Der V-Profilkran ist ein wirklich gutes Produkt. Wir haben daher sofort auf das neue Design gesetzt und sind nicht enttäuscht worden.“
Die Krane werden uns auch mit Blick auf die Zukunft gute Dienste leisten und sind mit 20 Tonnen Tragfähigkeit derzeit noch etwas größer dimensioniert. Wie wir aber zuletzt gelernt haben, werden unsere Maschinen immer größer und daher auch schwerer und ein Puffer in der Tragfähigkeit von 5 Tonnen stellte preislich keinen Unterschied dar.
Demag: Wie lösen Sie es, dass die Anlagen jederzeit verfügbar sind?
M. Schissele: Das vereinfachte Ersatzteilmanagement ist ein großer Vorteil. Wir bestellen eine große Anzahl von Ersatzteilen direkt über den Demag Shop. Ein schnelles und effizientes System, in dem man auch die Anzahl der KBK-Aufhängungen ersehen und sich Zeichnungen ausgeben lassen kann. Das ist eine richtig gute Sache. Und nach der Simulation kann ich die Produkte direkt bestellen. Das tun wir sehr oft und der Ablauf von der Informationsbeschaffung über die Auswahl bis zur Lieferung ist immer äußerst schnell. Früher habe ich mit dem Katalog effektiv und schnell die besten Produkte herausgefunden. Das hat sich durch den Shop nochmals vereinfacht.
Wir haben an beiden Produktionsstandorten ein Lager mit Demag Produkten und somit eine zentrale Ersatzteilversorgung. Dort lagern Produkte aus über 25 Jahren und fast alle sind miteinander kompatibel, das ist für uns ein enormer Vorteil und hilft dabei die Flexibilität zu wahren.
Demag: Haben Sie die Erweiterung der Fertigung auch über den Demag Shop geplant?
M. Schissele: Die Konfiguration von kleineren Projekten, ich benenne es jetzt einmal bis zu drei Kranen. Das geht ziemlich gut! Wenn ich ein komplettes Projekt habe, dann ist es immer besser, wenn man einen Partner hat, der uns unterstützen und mit dem man den Ablauf planen kann. Da war die Verkaufsmannschaft von Demag bei diesem Projekt sehr, sehr effektiv. Die Teile sind bei uns Sektor für Sektor angekommen. Die Teile waren so vorsortiert, dass alle benötigten KBK-Komponenten und Hebezeuge für den entsprechenden Sektor zusammengestellt waren. Wir haben vorab die Lieferzeiten besprochen und für jeden Zeitraum in den verschiedenen Kalenderwochen kamen die Pakete auf unsere Baustelle. Wir hatten dadurch kein großes Lager auf der Baustelle und unsere Mitarbeiter konnten die Anlage nach der Lieferung direkt montieren.
„Wir sind rundum zufrieden mit unseren Lösungen von Demag.“
Demag: Welche Vorteile sprechen für die eingesetzten Lösungen von Demag?
M. Schissele: Demag Produkte bieten eine große Flexibilität und ermöglichen die Herstellung komplexer Baugruppen auf einer kleinen Fläche. Die Langlebigkeit der Produkte ist sehr gut. Die Lastenaushaltung ist ebenfalls sehr gut und die einzelnen Komponenten kann man auch noch nach 20 oder 30 Jahren ohne Probleme nachbestellen. Unser hoher Anspruch an die Betriebssicherheit spiegelt sich zudem ebenso in den Produkten von Demag wider. Wir sind rundum zufrieden mit unseren Lösungen.
Demag: Welche Eindrücke haben Ihnen die Mitarbeiter über die Arbeit mit den Demag Produkte bisher geschildert?
M. Schissele: Die Mitarbeiter sind sehr zufrieden! Sie können die Komponenten mit einer hohen Geschwindigkeit transportieren. Der noch größere Vorteil besteht jedoch darin, dass die Positionierung für die Zusammensetzung von Baugruppen absolut präzise und effizient erfolgt. Sowohl mit den Leichtkransystem an den Arbeitsplätzen als auch mit den Kranen am Ende der Montagestraßen und im Versand.
Bildergalerie
Bildergalerie
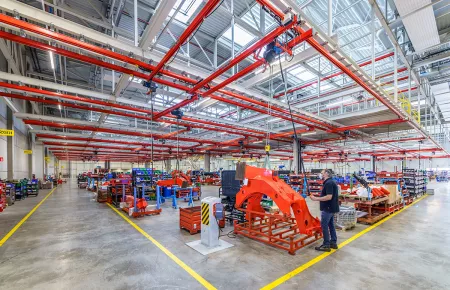
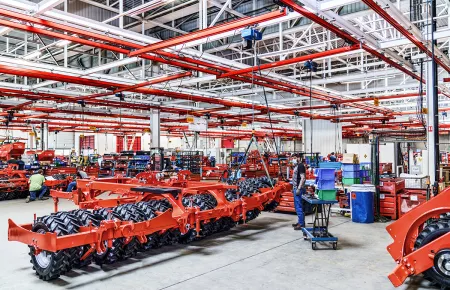
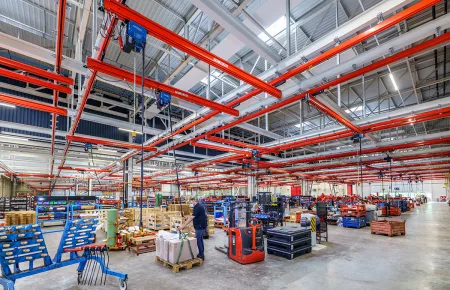
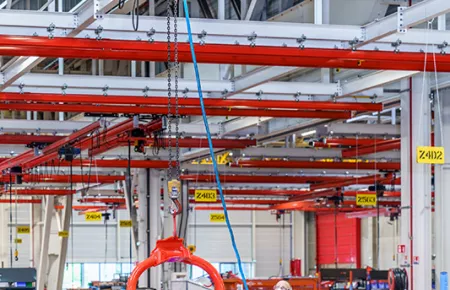